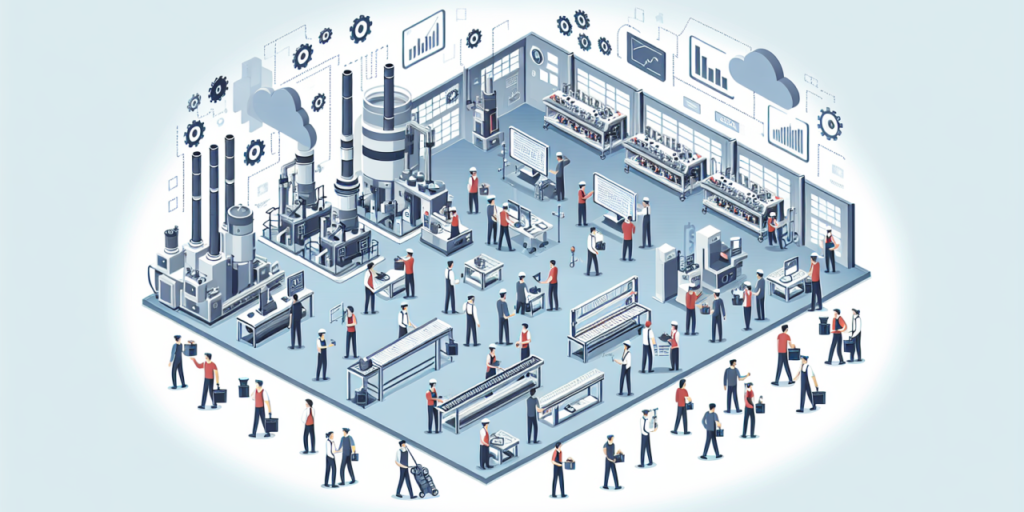
Sonic Air System has been a prominent player in the industrial drying and blow-off systems industry for four decades, known for their innovative and dependable solutions. Sonic Air Systems is a multinational company with operations in 40 countries. It specializes in creating customized solutions for a wide range of sectors. Their impressive selection of air knife systems and rapid centrifugal Sonic Air Blowers, which are made to accurately and successfully complete even the most difficult air-moving jobs, amply demonstrates their dedication to engineering excellence.
Sonic Air Systems was established with a focus on client satisfaction and technical innovation, and it has since developed into the ideal option for companies looking for superior air system solutions. The company’s capacity to provide complete technological solutions that maximize performance and minimize environmental effect, as opposed to just items, is what will determine how successful it is. Sonic is committed to improving operational performance across several industries, as seen by its dual focus on efficiency and sustainability, spanning from food and drink to pharmaceuticals and manufacturing.
Products from Sonic Air Systems generally comprise of original technologies and creative ideas that have set industry standards for energy economy and performance. Using decades of experience and a complete grasp of airflow dynamics, Sonic keeps inventing in drying and blow-off systems so insuring that every solution is tailored to match the individual needs of its customer base. This tailored approach is matched by a commitment to limited lead times, where standard blowers and air knives made in as little as five days redefine client delight and responsiveness.
Sonic Air Systems influences not just basic product delivery but also a full attitude to environmental responsibility. Sonic actively promotes sustainable manufacturing techniques by means of projects aimed at reducing energy use, so boosting resource economy, and so decreasing of greenhouse gas emissions. Their focus on alternative energy generation, recycling effectiveness, and trash repurposing emphasizes even more their part as ethical business people dedicated in environmental preservation.
Evidence of Sonic’s engineering prowess are his contemporary Test Lab Solutions, where possible customers may see personally the performance of air knife systems on their specific samples. This proactive approach not only ensures product efficacy but also provides potential consumers confidence, therefore highlighting Sonic’s continuous commitment to offer solutions above expectations.
Sonic Air Systems stands out in the packed sector of industrial air systems not just for unparalleled customer service but also for technological perfection. With 24/7 service coverage across the United States and beyond, Sonic promises that clients get speedy help and skilled advice wherever needed. This dedication to service quality as well as a solid product warranty with a money-back guarantee reflect Sonic’s confidence in the durability and efficacy of its products.
As air system technology continue to evolve, Sonic Air Systems remains poised to completely transform the industry. Sonic is determined to be a reliable partner for companies aiming to reduce their production costs and environmental impact while deepening their dedication to innovation and sustainability. Sonic Air Blowers is the top option for drying and blow-off systems among businesses worldwide who prioritize efficiency, dependability, and environmental responsibility.
Defining Lean Manufacturing
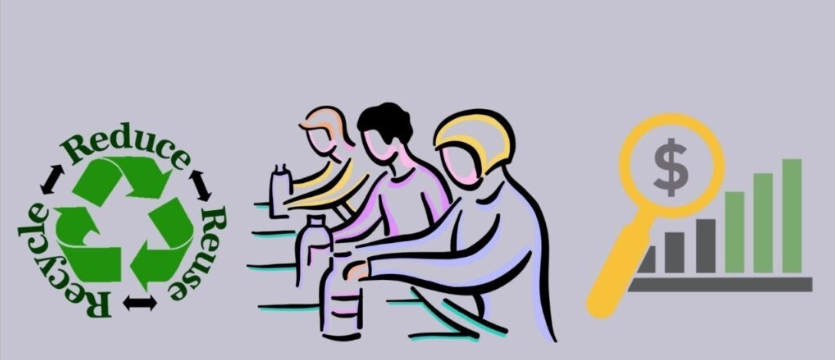
The idea of lean manufacturing, which is sometimes just referred to as “lean,” is to preserve value while requiring fewer labor. This technique focuses on improving the complete production process from start to finish rather than just lowering expenses or using fewer resources. Lean concepts promote value creation for clients by emphasizing ongoing development and the unwavering hunt for waste reduction.
Key aspects of lean manufacturing include:
- Maximizing customer value while minimizing waste.
- Understanding customer needs and expectations.
- Streamlining production processes.
- Improving quality and reducing time and cost.
The ultimate goal is to provide perfect value to the customer through a perfect value creation process that has zero waste.
The History and Evolution of Lean Practices
The Toyota Production System (TPS), created between 1948 and 1975 by Japanese industrial engineers Taiichi Ohno and Eiji Toyoda, is where lean manufacturing got its start. The first integrated system to concentrate on cutting waste in order to raise total customer value was the TPS.
The ideas behind TPS eventually gave rise to lean manufacturing as we know it today. These methods are now used in a number of industries besides the vehicle industry, such as services, construction, and healthcare. Just-in-time manufacturing, kanban systems, and kanban cards are examples of new technologies and processes that have been included into lean manufacturing as it has developed. These additions have improved the methodology and its applicability in many contexts.
An essential component of comprehending how lean manufacturing alters the dynamics of inventory and production management is comparing pull and push systems. Examining the origins and development of lean principles provides manufacturing managers with important insights into how to cut costs without sacrificing effectiveness or quality. Manufacturing managers are always looking to optimize operations and streamline processes. With an increasing focus on waste reduction and process optimization, lean manufacturing is redefining operational efficiency.
Core Principles of Lean Manufacturing
A methodical strategy to reducing waste and expediting production while producing high-quality goods that add value for consumers is known as lean manufacturing. It is supported by five fundamental ideas that help factory managers maximize productivity.
Finding Value from the Viewpoint of the Customer
Understanding what value means to the customer is the first lean manufacturing principle. In order to do this, it is necessary to comprehend client demands and define value in response to them. By doing this, producers may make sure that each stage of the manufacturing process enhances the final product’s perceived value for the consumer.
Lean manufacturing’s foundation is value identification. It establishes what constitutes and does not constitute waste. Elimination of products and procedures that do not provide value for the client is a possibility.